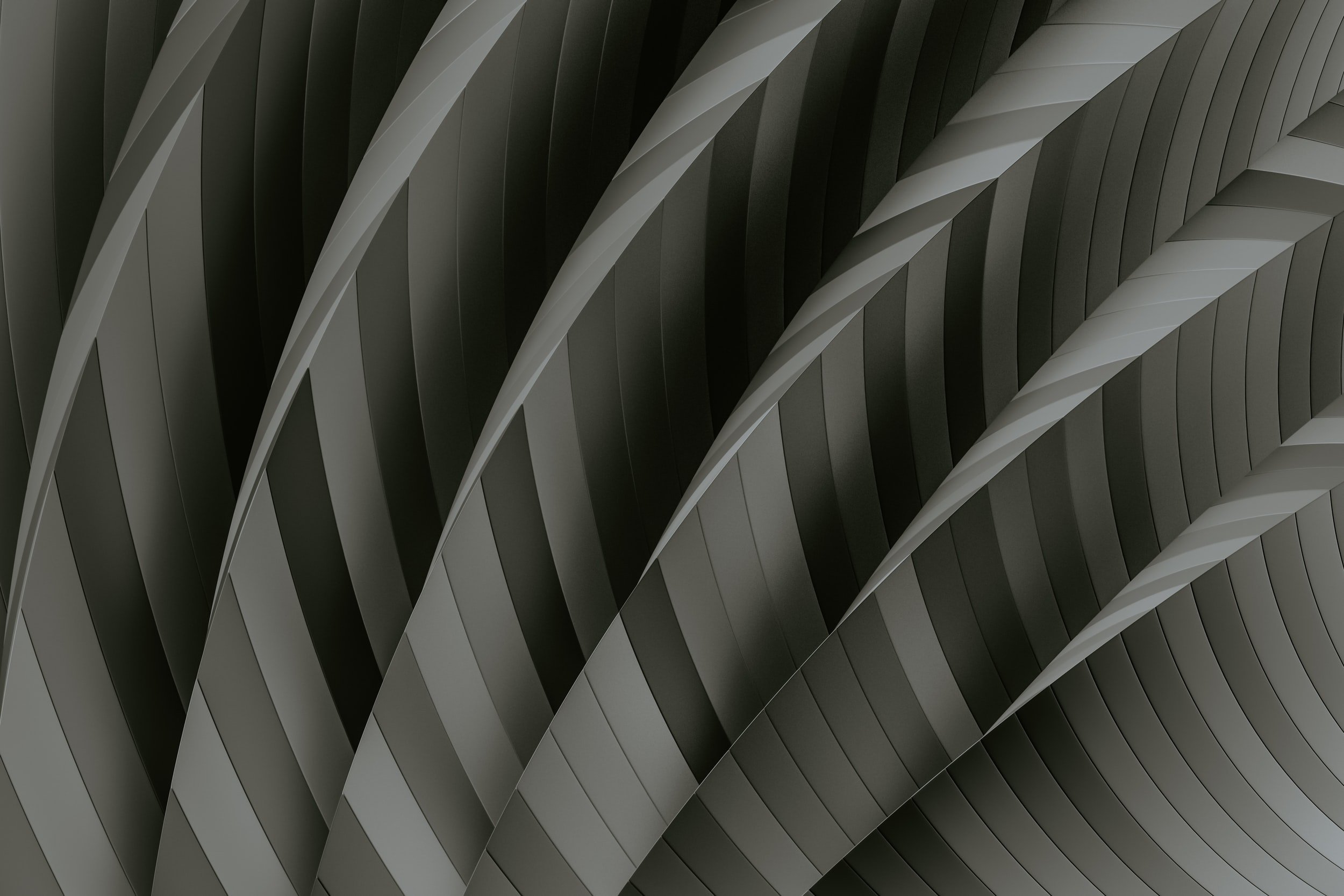
“You never change things by fighting the existing reality. To change something, build a new model that makes the existing model obsolete.”
Buckminster Fuller
The Global Building Challenges
Every economy on earth is challenged by the rise of the human population and climate change. To accommodate the extra people, we'll need to construct the equivalent of a new metropolis every five days between now and 2050.
To make our cities sustainable and financially viable, we must transition to a circular economy, carbon neutrality, and net zero.
Design, engineering, and building procedures are only one aspect of the problem; other elements include a new business model, workflow, knowledge management systems, supply chains, and product lifecycle management.
The Outdated Architecture, Engineering & Construction (AEC) industries
We are failing miserably in every way!
Since a century ago, there hasn't been a substantial advance in the AEC industry. And yet, we continue to use the same outdated techniques while developing on-site. It is labour-intensive, very inefficient, incorrect, dangerous, and wasteful.
Businesses spend a lot of time shifting blame and raising prices to account for risk. It causes a race to the bottom regarding housing performance and quality.
The Analogue Knowledge-Economy
A network of consultants requests and manually produces design, engineering, and construction information. It is a prohibitively long-consuming, expensive, hazardous, and opaque process that involves a lot of guessing, misunderstandings, competing interests, and repeated time spent working to solve the same issues.
The Fragmented Services & Supply Chains
The AEC Industries are highly fragmented, adversarial, risk-averse design and supply chains. Companies spend much time pushing liability blame onto each other and up-pricing for risk.
The procurement approaches isolate these expenses to developers and contractors, raise prices and lead to a race to the bottom on performance and quality.
Why hasn’t technology solved this problem?
Even if the AEC Industries collaborate using BIM, this paper-based, file-trading paradigm still exists. We still create and distribute files manually. This is because instead of restructuring the supply chain, the business models of BIM and CAD software businesses dictate that they offer proprietary desktop software to the currently segregated professions.
The Unproductive RIBA Sequential Work Methods
The format of the RIBA Sequential Methods is linear. The several phases are completed one after the other, with all attention and resources directed into that undertaking. Once a Stage is finished, it is left in peace while attention is given to the stage after that. It takes a while and frequently results in labour-intensive design revisions, which delays projects and puts financial strain on all parties.
The Risk of Sequential Work Methods
Developers’ Nightmare
“Of every £1 spend, just over 51% is retained in residual asset value!”
According to a recent government examination of projects completed under their construction framework, only around half of the construction budget for a typical project is left as the residual value in the finished good. The remaining money is used for:
The risk inherent in the design and construction method
Architects & Engineers have no responsibility for costing
Typical value-engineering strategies are no longer accurate
Fees for the various designers & consultants involved
Profit and overheads for the various parties involved
Poor productivity
Operational stoppage
Skilled & competent labour shortage
Material shortage & fluctuations
Lack of design information & communication
Average 20% hidden cost of every project
How Aerospace & Automotive Industries work with DfMA approach?
Reduced Development Time: By considering manufacturing and assembly aspects early in the design process, both industries can significantly reduce product development time.
Enhanced Collaboration: DfMA fosters closer collaboration between design, engineering, and manufacturing teams, leading to more efficient and feasible product designs.
Adaptability to New Technologies: As both industries evolve with new technologies, DfMA provides a framework to integrate these innovations effectively into product designs.
The Digital Industrial Revolution
Our industries, society, economy, and the built environment have all undergone a drastic change due to the Digital Industrial Revolution, which is still in its early phases.
KREOD technology and workflow offer fundamental changes in the AEC Industries.
KREOD Integrated Concurrent Engineering Workflow
KREOD Integrated DfMA Intelligent Automation (KIDIA) software allows different design stages to run simultaneously rather than consecutively. It automatically generates manufacturing/fabrication code and Bill of Materials (BOM) for a transparent & accurate costing at the Concept Design Stage. It simplifies RIBA Stages 2, 3 & 4 and saves up to 90% of the time.
KREOD Solutions
KREOD Integrated Smart Solutions (KISS) Platform and KREOD Integrated DfMA Intelligent Automation (KIDIA) software allow different design stages to run simultaneously rather than consecutively.
KIDIA automatically generates manufacturing or fabrication code and Bill of Materials (BOM) for a transparent & accurate costing at the Concept Design Stage. It simplifies the RIBA stages 2, 3 & 4 and saves up to 90% of the time.
The benefits are:
Intelligent, Certain, Efficient, Accurate & Competitive
Maximise residual asset whole-life value
Eliminate or minimise risk and setbacks
Create flexible components that can be used across programmes for a variety of building types
Facilitate highly planned and coordinated logistics from manufacture and supply chain through to activities on site
Use low-skilled or unskilled labour from design, engineering, and manufacturing to construction (as the process is automated with KREOD Intelligent Automation Tools)
The fewest number of people to assemble the lightweight KREOD Aeronautics Building Systems (KABS)
Simulation - Prior to construction, we simulate the construction process, i.e. logistics, handling, construction sequencing
KREOD Construction Sequencing & Management Tool
No weather dependant on assembly
Construction speed is up to 50% faster than the traditional method
Reduces site waste by 70 to 90%
Lower costs due to speed and efficiencies
Levelling up - better design & higher quality building materials that no contractor can compete with KREOD